Boosting Industrial Automation Realtime Performance with Machine Vision Computers and EtherCAT Connectivity
Machines and robots in industrial automation are becoming increasingly intelligent with the integration of vision technology. As factories and manufacturing systems advance, machine vision allows robots and machines to “see” and make informed decisions in real-time. By integrating machine vision computers with EtherCAT communication, you can achieve higher precision and faster processing, crucial for tasks like robotic assembly, quality inspection, and object recognition. These systems not only boost your productivity but also enable more complex and synchronized automation, transforming the way you manage industrial operations.
The NP-6113-ECATS from Nodka is an excellent example of how integrating machine vision with EtherCAT slave functionality can optimize performance in real-time applications. Unlike traditional machine vision PC solutions, which rely on TCP/IP Ethernet-based communication between the automation controller and the machine vision system, the NP-6113-ECATS uses EtherCAT’s deterministic, real-time communication protocol. In standard systems, reliance on custom protocols or TCP/IP for communication can introduce challenges, such as higher latency and more complex integration for system developers. Custom protocols often require additional configuration and troubleshooting, which can lead to delays and inefficiencies. However, with EtherCAT, integrators benefit from a standardized, high-speed communication framework designed for industrial automation. This enables faster and more reliable interactions between the vision system and controllers, significantly improving precision and speed of operations, making it ideal for demanding tasks like robotic control, quality inspection, and object recognition.
Key Features of the NP-6113-ECATS:
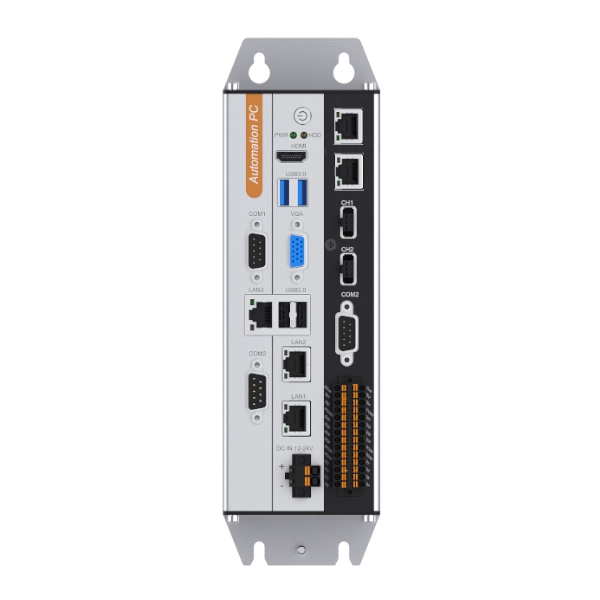
The NP-6113-ECATS is equipped with several standout features designed to enhance machine vision applications in industrial automation:
- 3× Intel i210 GbE LAN controllers, two of which support Power over Ethernet (PoE)
- 2× Light control interfaces with support for hard trigger
- 8 isolated digital inputs (DI) and 8 isolated digital outputs (DO)
- 1× EtherCAT Slave port, which supports 480 input PDOs and 480 output PDOs
Additionally, the NP-6113-ECATS offers comprehensive SDK support for both Windows and Linux platforms:
- ESI file for easy configuration of the EtherCAT slave
- SDK for DIO and Light control
- SDK for EtherCAT slave communication
Why EtherCAT and Machine Vision Are a Powerful Combination
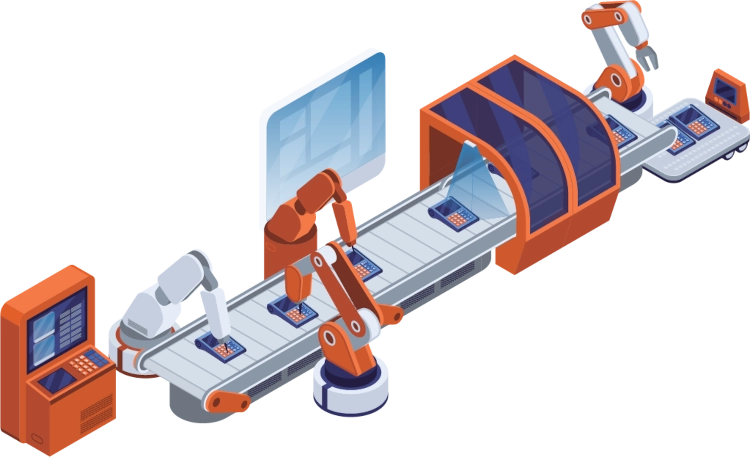
Real-Time Communication for Precision Control
EtherCAT’s deterministic communication ensures that data between your machine vision computer and the robot arm controller is exchanged with minimal delay. The EtherCAT slave port on the NP-6113-ECATS, supporting up to 480 input and output PDOs, allows for fast, reliable data transmission. This makes the system perfect for applications like robotic assembly and quality inspection, where real-time feedback ensures accurate, on-the-fly adjustments.
Decoupling of Vision and Control Systems
The NP-6113-ECATS provides modular design flexibility by decoupling machine vision processing from the main control system. With isolated digital inputs and outputs, you can ensure that your system operates without interference, allowing for easy integration into complex industrial setups without disrupting your control architecture.
Seamless Integration with Existing Automation Systems
The NP-6113-ECATS integrates effortlessly into existing EtherCAT-based networks, simplifying the setup process while ensuring compatibility with other devices. The PoE support from the LAN controllers also enables easy power delivery for cameras or other peripherals without the need for additional wiring.
High-Speed Data Processing for Complex Tasks
Machine vision tasks, such as object recognition and defect detection, require high-speed data transfer, which is facilitated by the NP-6113-ECATS’s Intel GbE LAN controllers and EtherCAT slave communication. This allows your system to handle large amounts of visual data in real-time, ensuring faster and more precise decisions on the factory floor.
Improved Synchronization and Coordination
EtherCAT’s distributed clocks provide precise synchronization across devices. The light control hard trigger feature of the NP-6113-ECATS allows for synchronized illumination, which is critical for high-precision tasks such as optical inspections and 3D scanning.
Real-World Application Example: Robot Arm Control with Machine Vision
In a robotic arm application, the NP-6113-ECATS can be used to guide the robot’s movements based on real-time visual data. For example, when your robot is tasked with picking items from a conveyor belt, the machine vision system captures images of the items and identifies their exact location and orientation. The EtherCAT connection ensures that this data is transferred to the robot controller without delay, allowing the robot to accurately pick and place items. If items are positioned differently, the robot can adjust its actions in real-time based on continuous feedback from the vision system.
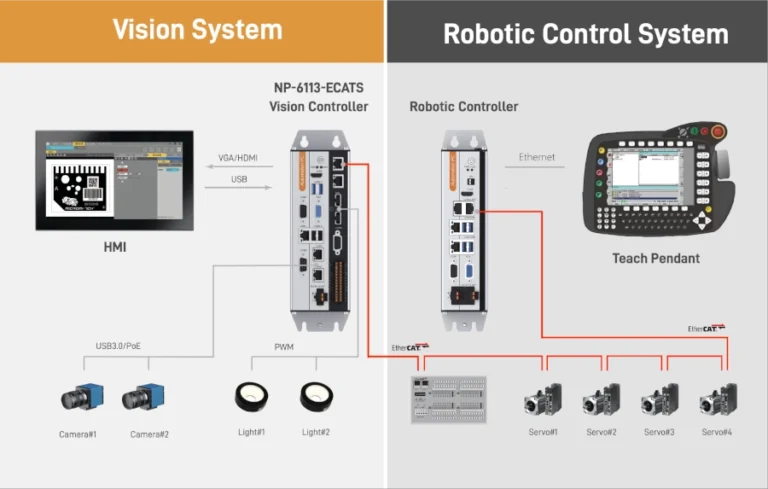
In this scenario, the NP-6113-ECATS machine vision computer acts as the EtherCAT slave, sending visual data to the robot arm controller (the EtherCAT master). The high-speed, deterministic communication enabled by EtherCAT ensures that the robot’s movements are precise and in sync with the real-time vision feedback, improving both speed and accuracy in your production process.
About the Application Diagram:
The NP-6113-ECATS machine vision computer functions as an EtherCAT slave in a setup designed for real-time industrial automation tasks, such as visual inspection or object detection during robotic operations. The robot arm controller, on the other hand, is the EtherCAT master.
Key Components and Workflow:
The processed visual data from the NP-6113-ECATS is critical for the robot arm’s task execution, allowing it to adjust its actions based on real-time machine vision inputs, such as picking, placing, or inspecting items.
Robot Arm Controller (EtherCAT Master):
This controller manages the overall coordination and operation of the robot arm. As the EtherCAT master, it initiates communication cycles and sends instructions to the connected devices, including the NP-6113-ECATS.
The controller processes commands and controls the robot’s movements based on input from external systems like machine vision.
NP-6113-ECATS (EtherCAT Slave):
The NP-6113-ECATS machine vision computer is responsible for capturing and processing visual data, such as recognizing objects or identifying defects.
Acting as an EtherCAT slave, it receives timing signals from the robot arm controller, processes the visual data in real-time, and sends back the necessary feedback (e.g., object positioning or quality data) to the master.
Communication:
EtherCAT provides fast and synchronized communication between the robot arm controller (master) and the NP-6113-ECATS (slave). This ensures that visual data is processed quickly and efficiently, allowing for precise, real-time adjustments to the robot arm’s movements.
With the NP-6113-ECATS, Nodka continues to push the boundaries of industrial PCs in industrial automation, providing you with cutting-edge solutions to meet the demands of today’s fast-paced production environments. Talk to us about how Nodka can customize our automation PC solutions to meet your specific machine vision needs.